Stand Out During Your Die Casting Job Interview. Job interviews often give some applicants a scary impression. Thinking if their interviewers would like them or not decreases their confidence that is suppose to show up during this formal, yet fun …
Continue reading
Category Archives: Diecasting Process
Die Casting Driving Innovation
Die Casting Revolutionizes Car Parts Manufacturing, where performance, efficiency, and safety are paramount, the quality and precision of every component can make all the difference. Enter die casting, a manufacturing process that has revolutionized the production of car parts, offering unmatched precision, versatility, and efficiency. From engine components to structural elements, transmission housings to suspension components, die casting plays a pivotal role in shaping the future of automotive engineering. Let’s explore how die casting has transformed the manufacturing landscape of car parts and its profound impact on the automotive industry.
Strength and Lightweight Design. In the pursuit of fuel efficiency and performance, automotive engineers are constantly seeking ways to reduce vehicle weight without compromising strength and durability. Die casting provides an ideal solution, allowing manufacturers to produce lightweight parts with exceptional structural integrity. Aluminum and magnesium alloys, commonly used in die casting, offer a winning combination of strength and weight savings, making them well-suited for automotive applications. By leveraging die casting techniques, car manufacturers can design and fabricate components that enhance fuel efficiency, increase payload capacity, and improve overall performance.
The engine serves as the heart of any vehicle, relying on a multitude of precision-engineered components to deliver power efficiently and reliably. From cylinder heads and engine blocks to intake manifolds and transmission cases, die casting plays a critical role in the production of these vital parts. By utilizing die casting processes, automotive manufacturers can achieve the tight tolerances and intricate geometries required for optimal engine performance. Moreover, die casting enables the production of complex shapes and features that would be difficult or impossible to achieve using traditional machining methods, further enhancing engine efficiency and reliability.
Safety is a top priority in automotive design, and vehicle structures must withstand the forces encountered during normal operation and in the event of a collision. Die casting enables the production of parts with uniform grain structure and minimal porosity, resulting in enhanced mechanical properties and crashworthiness. Whether it’s chassis components, suspension parts, or body reinforcements, die-cast parts contribute to the overall strength and safety of vehicles, ensuring passenger protection and structural integrity.
The transmission and drivetrain systems are critical to the performance and efficiency of vehicles, requiring precision-engineered components to transfer power smoothly and reliably. Die casting is instrumental in the production of transmission housings, differential cases, and gearbox components, providing the strength, dimensional accuracy, and heat dissipation capabilities necessary for optimal performance. By leveraging die casting techniques, automotive manufacturers can achieve the intricate geometries and complex features required for advanced transmission systems, improving overall drivability and fuel efficiency.
As automotive technology continues to evolve, so too does the role of die casting in shaping the future of vehicle manufacturing. Manufacturers and engineers collaborate to push the boundaries of innovation, leveraging advanced materials, design optimization techniques, and cutting-edge manufacturing processes to meet the evolving needs of the automotive industry. From lightweight structural components to high-performance engine parts, die casting remains at the forefront of automotive innovation, driving progress and shaping the next generation of vehicles.
Die casting has revolutionized the manufacturing of car parts, offering automotive manufacturers the precision, efficiency, and reliability required to meet the demanding standards of the industry. From enhancing fuel efficiency to improving vehicle safety, die-cast parts play a vital role in shaping the future of automotive engineering, ensuring that vehicles continue to drive innovation and performance on the road ahead.
Permalink: https://www.kineticdiecasting.com/kdc/die-casting-driving-innovation/
“The Parts We Make Today, We Ship Today”
Kinetic Die Casting Company. Inc.
6918 Beck Avenue, North Hollywood,
California 91605, United States of America
E-mail sales@kineticdc.com
USA Toll Free: (800) 524-8083 Local: (818) 982-9200
To get prices for Die Casting Car Parts:
Quote Car Parts Die Casting Prices
Kinetic Die Casting Company makes:
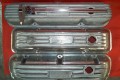
Die Casting Bracket Hardware
Airplane Die Casting Parts
The Importance of Die Casting Draft Angles
In die casting, when precision meets efficiency, every detail matters. Among the many factors that contribute to the success of the die casting process, the draft angle stands out as a crucial consideration. Often overlooked but essential, the draft angle plays a pivotal role in ensuring the manufacturability, quality, and integrity of die-cast parts. Let’s delve into the significance of draft angles in die casting and the strategies employed to optimize their impact on the production process.
Understanding Draft Angles in die casting, a draft angle refers to the taper or slope applied to vertical walls or surfaces of a mold cavity. It facilitates the removal of the casting from the mold after the casting process is complete. By incorporating draft angles into the design of die-cast parts, manufacturers can prevent damage to the part and the mold, reduce the likelihood of defects, and ensure smoother ejection during demolding. The primary function of draft angles is to facilitate the ejection of the casting from the mold cavity. Without proper draft angles, the casting may become wedged or stuck within the mold, leading to deformation, surface defects, or even mold damage during the demolding process. By providing a gradual taper to the walls of the mold, draft angles allow for easy and consistent removal of the casting, minimizing the risk of costly rework or production delays. Draft angles also play a crucial role in preventing undercuts, which occur when features of the part prevent it from being extracted straight out of the mold. Without adequate draft angles, undercuts can result in the formation of undesirable features such as flash or distortion on the casting, compromising its dimensional accuracy and surface finish. By incorporating draft angles into the design, engineers can mitigate the risk of undercuts and ensure smooth demolding of the part. Proper draft angles contribute to the overall surface finish of die-cast parts. By allowing for smooth ejection from the mold cavity, draft angles help minimize friction and shear forces that can result in surface imperfections such as scratches, blemishes, or parting lines. Additionally, draft angles promote uniform cooling of the casting, reducing the likelihood of thermal gradients and associated defects, thus enhancing the final surface quality of the part.
While draft angles are primarily functional considerations, they also have implications for the aesthetics of die-cast parts. Careful attention to draft angles can help maintain the visual integrity of the part by minimizing the appearance of parting lines, flash, or other defects. By striking the right balance between functionality and aesthetics, designers can ensure that die-cast parts not only perform optimally but also meet the visual standards expected by customers.
Die Casting Draft Angles are a critical aspect of die casting design, influencing the manufacturability, quality, and aesthetics of die-cast parts. By incorporating proper draft angles into the design process, manufacturers can optimize the die casting process, minimize production issues, and ensure the successful production of high-quality parts. As die casting continues to evolve and innovate, draft angles will remain an essential consideration in achieving precision, efficiency, and excellence in manufacturing.
“The Parts We Make Today, We Ship Today”
Kinetic Die Casting Company. Inc.
6918 Beck Avenue, North Hollywood,
California 91605, United States of America
E-mail sales@kineticdc.com
USA Toll Free: (800) 524-8083 Local: (818) 982-9200
To get prices for Die Casting Parts:
Request Die Casting Part Prices
Kinetic Die Casting Company makes:
NADCA-Product-Standards-for-Die-Casting-pdf
Die Casting Porosity
Die Casting Draft Angle
The Versatility of Aluminum and Sand Casting Parts in Modern Manufacturing
The Versatility of Aluminum and Sand Casting Parts in Modern Manufacturing
In the realm of modern manufacturing, the utilization of aluminum and sand casting parts has become integral to the production of a wide array of products across various industries. The versatility, durability, and cost-effectiveness of aluminum, combined with the flexibility and intricacy of sand casting processes, have made this combination a go-to choice for many manufacturers looking to create high-quality components.
**Aluminum: The Material of Choice**
Aluminum stands out as a favored material for manufacturing due to its exceptional properties. Its lightweight nature, excellent corrosion resistance, high strength-to-weight ratio, and ability to be easily machined make it an ideal choice for a multitude of applications. From automotive parts to aerospace components, aluminum’s versatility knows no bounds.
One of the key advantages of aluminum is its ability to be recycled repeatedly without losing its inherent properties. This sustainability factor not only reduces manufacturing costs but also aligns with the growing emphasis on environmentally friendly practices in the industry.
**Sand Casting: A Time-Tested Technique**
Sand casting, one of the oldest known metal casting processes, complements the properties of aluminum perfectly. This versatile technique involves using a mold made of compacted sand to shape molten metal into a desired form. The flexibility of sand casting allows for the production of complex geometries and intricate designs, making it ideal for creating unique components that often cannot be achieved through other manufacturing methods.
The process of sand casting offers several advantages, including cost-effectiveness, suitability for both small and large production runs, and the ability to quickly create prototypes for testing and validation. Its adaptability to a wide range of alloys, including aluminum, further enhances its appeal in modern manufacturing.
**The Synergy of Aluminum and Sand Casting Parts**
The combination of aluminum and sand casting parts unlocks a realm of possibilities for manufacturers seeking high-quality, bespoke components. Aluminum’s exceptional properties, such as its strength, corrosion resistance, and thermal conductivity, make it an excellent choice for a diverse range of applications, including automotive, aerospace, marine, and industrial sectors.
By harnessing the intricacies of sand casting, manufacturers can achieve precision and detail in their aluminum parts, ensuring that each component meets the exact specifications required for optimal performance. The ability to produce components with thin walls, complex shapes, and tight tolerances underscores the synergy between aluminum and sand casting in delivering top-tier products.
Furthermore, the cost-effectiveness and efficiency of the aluminum and sand casting combination make it a preferred choice for manufacturers looking to streamline their production processes while maintaining high standards of quality.
**In Conclusion**
In the landscape of modern manufacturing, the union of aluminum and sand casting parts stands as a testament to innovation, quality, and efficiency. The remarkable properties of aluminum, coupled with the flexibility and precision of sand casting processes, create a harmonious synergy that enables the production of superior components across a multitude of industries. As technology advances and demands for intricate and reliable components grow, the role of aluminum and sand casting in shaping the future of manufacturing remains pivotal.
“The Parts We Make Today, We Ship Today”
Kinetic Die Casting Company. Inc.
6918 Beck Avenue, North Hollywood,
California 91605, United States of America
E-mail sales@kineticdc.com
USA Toll Free: (800) 524-8083 Local: (818) 982-9200
To get price quotes for Die Casting Tooling Molds or Die Casting Parts:
Quote Die Casting Prices
Kinetic Die Casting Company makes:
Automotive Die Casting Parts
Die Casting Bracket Hardware
Airplane Die Casting Parts
Aluminum Machining Differs from Steel Parts Machining in 2023
Aluminum Parts Machining Differs from Steel Parts Machining. Aluminum can be used in many ways. However there are different ways on how you can work with it. Aluminum parts machining requires less power compared to steel parts or cast iron parts because they are light weight.
Aluminum parts machining can be different in cast iron machining. It’s the type of tools and tooling technologies that you will use will make a difference.
Kinetic Die Casting Company makes aluminum die cast parts. If you are working with aluminum parts, the spindle of the machine should be strong and forceful. Spindles require higher speeds along with a lesser low-end torque compared to machining other metals like steel. Also, the spindle should be stiff because it will work in very fast conditions. Other experts on this field recommend the use of HSK tapers to ensure accuracy and rigidity. Moreover, if you are using very fast tools, rotating inertia can be reduced with the use of closed-loop spindles powered by a motor.
Furthermore, it requires little cutting forces if you are working out with aluminum parts. The machine has to be well-damped and stiff.
Since you are working with high speeds, there’s a chance of thermal growth. It can create a major problem if you are working out with light metals. It can lead to a major problem if you are working with light metal parts like aluminum.
Find yourself a machine with thermal control system. A cooling system is recommended in order to reduce the frictional heat in the bearings when the higher spindle speeds up. Also, you must protect the spindle against coolant penetration by sealing it because the entire machining operation of a light metal is not dry.
Kinetic Die Casting manufactures products like aluminum hardware, and aluminum boxes. If you would like more information on Kinetic Die Casting, please visit our website:Kinetic Die Casting Company
“The Parts We Make Today, We Ship Today”
Kinetic Die Casting Company. Inc.
6918 Beck Avenue, North Hollywood,
California 91605, United States of America
E-mail sales@kineticdc.com
USA Toll Free: (800) 524-8083 Local: (818) 982-9200
To get prices for Die Casting Tooling Molds or Parts:
RFQ Die Casting Tooling Part Prices
Kinetic Die Casting Company makes:
Does Thicker Walls in Die Casting create Stronger Die Cast Parts in 2023?
Kinetic Die Casting Company has helped many customers develop new products. There are many factors singular to the die casting process that are needed to consider such as product strengths, draft angles, gate areas, material types, material flow, slide features, undercuts, and wall thicknesses.
Over the years, I have had to convince several buyers, engineers, and designers that increasing the thickness of the walls or other sections in a die casting part does not increase the part strength. In fact, it does the opposite. As the molten metal is injected through the gate, into the die casting mold, the metal freezes on the wall surfaces of the die on the die casting part exterior and interior. The metal contacting these die surfaces is denser and harder than the section sandwiched between the two wall surfaces.
The first .030” to .050” surface of the casting where the metal is denser is commonly called the “skin” of the die casting. The die casting skin is on both interior surfaces and exterior surfaces. The material between the two skin surfaces is weaker and less dense. A part that has a wall thickness of .080” would have a skin surface of about .060”, on the interior wall .030” and the exterior wall .030”. The section sandwiched between the two skins, approximately .020” would provide little strength.
Die Casting parts should not typically be thicker than .125”. On die casting parts with thicker walls than .125”, the increased thickness decreases the wall strength by increasing opportunities for porosity, shrinkage and laps. Parts that will be machined should only have less than .030” removed to preserve more of the die casting strength and to avoid exposing porosity.
When it comes to increasing strength in aluminum die casting parts, other methods are used. I will detail how to strengthen die casting parts in future articles.
Contact Kinetic Die Casting Company 800-524-8083, if you have a metal product that you are considering manufacturing. We will evaluate your design and make suggestions on other metal manufacturing processes when necessary. If die casting is the best option, we will assist you in material selection, tooling manufacture, and provide the cost for tooling and die casting parts.
Kinetic Die Casting manufactures custom metal parts to their customer. If you would like more information about Kinetic Die Casting, please visit our website:Kinetic Die Casting Company
“The Parts We Make Today, We Ship Today”
Kinetic Die Casting Company. Inc.
6918 Beck Avenue, North Hollywood,
California 91605, United States of America
E-mail sales@kineticdc.com
USA Toll Free: (800) 524-8083 Local: (818) 982-9200
To get prices for Die Casting Tooling Molds or Parts:
RFQ Die Casting Tooling Part Prices
Kinetic Die Casting Company makes: