Aluminum Auto Parts – What Every Car Needs. Hundreds and thousand of aluminum auto parts are being produced by different die casters everyday. Aside from the design’s lightweight element, most aluminum auto parts are also being carefully constructed as net …
Continue reading
Category Archives: Auto Parts
Zinc Die Cast Auto Parts
Zinc die cast auto parts have revolutionized the automotive industry, offering a perfect combination of durability, precision, and cost-efficiency. As a popular choice for manufacturing various automotive components, zinc die casting provides exceptional strength and corrosion resistance that meet the high demands of the automotive sector.
The process of zinc die casting involves injecting molten zinc metal under high pressure into a steel mold cavity, allowing intricate and complex shapes to be produced with excellent dimensional accuracy. This manufacturing method enables the production of auto parts with thin walls, fine details, and tight tolerances, making zinc die casting a preferred option for a wide range of automotive applications.
One of the key advantages of using zinc die cast auto parts is their superior strength-to-weight ratio. Zinc alloys, such as Zamak, offer high strength and rigidity, making them ideal for producing lightweight yet robust components for automotive vehicles. This strength ensures that zinc die cast auto parts can withstand the rigors of daily use, providing long-lasting performance and reliability.
In addition to their strength, zinc die cast auto parts also exhibit excellent corrosion resistance, making them well-suited for use in various automotive environments. The inherent properties of zinc alloys prevent rust and deterioration, ensuring that auto parts remain in optimal condition even under harsh conditions like exposure to moisture, chemicals, or temperature fluctuations. This corrosion resistance enhances the longevity and durability of zinc die cast auto parts, making them a cost-effective choice for automotive manufacturers.
Furthermore, zinc die casting offers exceptional design flexibility, allowing auto parts to be produced in a wide range of shapes and sizes to meet specific performance requirements. The ability to create intricate geometries and complex features through zinc die casting enables automotive designers to optimize product designs for functionality, performance, and aesthetics. This versatility in design allows for the production of customized auto parts that can enhance the overall performance and appearance of vehicles.
Another significant advantage of zinc die cast auto parts is their cost-efficiency. The high productivity and repeatability of the die casting process result in lower production costs compared to other manufacturing methods. The fast cycle times and minimal post-processing required for zinc die casting further contribute to reducing overall production costs, making it an economical choice for automotive manufacturers looking to maximize efficiency and profitability.
Additionally, the recyclability of zinc alloys used in die casting makes zinc die cast auto parts an environmentally sustainable option for automotive applications. Zinc is a fully recyclable material that can be melted down and reused without degradation in quality, reducing the environmental impact of manufacturing processes and promoting a circular economy approach within the automotive industry.
In conclusion, zinc die cast auto parts offer a winning combination of strength, durability, corrosion resistance, design flexibility, cost-efficiency, and sustainability that make them an ideal choice for automotive manufacturers. With their unmatched performance and reliability, zinc die cast auto parts play a crucial role in enhancing the safety, efficiency, and overall quality of vehicles on the road.
“The Parts We Make Today, We Ship Today”
Kinetic Die Casting Company. Inc.
6918 Beck Avenue, North Hollywood,
California 91605, United States of America
E-mail sales@kineticdc.com
USA Toll Free: (800) 524-8083 Local: (818) 982-9200
To get prices for Die Casting Tooling Molds or Parts:
RFQ Die Casting Tooling Part Prices
Kinetic Die Casting Company makes:
Metal Casting Parts or Plastic Parts
Military Die Casting Parts
Die Casting Tooling
Permalink: https://www.kineticdiecasting.com/kdc/zinc-die-cast-auto-parts/
American Auto Die Castings
Processing Motor Vehicle Die Cast Parts. Many American automotive parts companies are now using die casting. It is a metal-working procedure which is intended for large scale productions. Motor vehicle die cast parts are known for ease in production and performance against multi-directional stresses. These parts are used as stationary parts like the vehicle frame and engine fixtures. They are also intended for mechanical parts like gears, engines and chains.
Die casting and its variants always compress molten or semi-molten metals. Hence, pressure and temperature are always important factors. As for motor vehicle die cast parts, they are usually created through cold chamber die casting. The type of casting depends on the type of metal. Majority of metal products in the automotive industry utilize aluminum and magnesium. Cold chamber method is the one appropriate for such high-melting point metals.
The metal is melted in a separate furnace. As it is cooling down, it will be transported to the dies, which contain the target shape. Depending on the strength specifications and type of metal, pressures between 10 to 175 mPa will be maintained until the metal solidifies. This can produce a wide range of shapes from the simple to the intricate: rods, bars, billets, planes and fixtures. They require little or no post machining because die casting results in precise shapes and thickness.
Motor vehicle die cast parts include engine blocks and some gears, which are mostly made of aluminum and magnesium casts. The combination of these two metals is very tough, even when subjected to repeated load and high temperatures.
To get a price for aluminum die casting parts or die casting tooling, call toll free 800-524-8083 and ask for sales. Or email us at sales@kineticdc.com for a fast response on a price quote.

Kinetic Die Casting manufactures zinc and aluminum die casting. If you would like a quote, please visit our website:Die Casting quote
https://www.kineticdiecasting.com/kdc/processing-motor-vehicle-die-cast-parts/
Zinc Die Cast Knobs
Zinc die-cast knobs are essential components in various industries, offering durability, versatility, and aesthetic appeal. With excellent strength and corrosion resistance properties, zinc die-cast knobs have become a popular choice for manufacturers due to their ability to withstand both indoor and outdoor applications. This article will delve deeper into the characteristics, benefits, applications, and considerations of zinc die-cast knobs in the manufacturing sector.
Zinc die-cast knobs are manufactured through a process called die casting, which involves injecting molten zinc into a steel mold cavity under high pressure. This process allows for the production of intricate and precise designs, making zinc die-cast knobs a versatile option for various applications. The use of zinc as a base material also contributes to the knobs’ strength and resistance to wear and tear, ensuring a long lifespan even in demanding environments.
One of the key advantages of zinc die-cast knobs is their aesthetic appeal. The material can be easily plated or coated with various finishes, including chrome, nickel, or powder coating, to match different design requirements. This versatility in finishing options allows manufacturers to tailor the appearance of zinc die-cast knobs to suit a wide range of products, from industrial machinery to consumer electronics.
In addition to their visual appeal, zinc die-cast knobs offer excellent tactile feedback and ergonomic functionality. The knobs can be designed with different shapes, sizes, and textures to provide users with a comfortable grip and precise control. This makes zinc die-cast knobs ideal for applications where precise adjustment or manipulation is required, such as in instrumentation panels, control systems, or consumer appliances.
Another significant benefit of zinc die-cast knobs is their cost-effectiveness. The die-casting process allows for high production volumes at a relatively low cost per unit, making zinc die-cast knobs a cost-efficient solution for manufacturers looking to scale up their production. Furthermore, the durability and longevity of zinc die-cast knobs reduce maintenance and replacement costs, providing long-term value for businesses.
Zinc die-cast knobs find wide applications across various industries, including automotive, electronics, furniture, and machinery. In the automotive sector, zinc die-cast knobs are used in dashboard controls, door handles, and HVAC systems, providing drivers with reliable and durable components. In the electronics industry, zinc die-cast knobs are commonly found in audio equipment, home appliances, and industrial machinery, where precision and durability are paramount. When considering zinc die-cast knobs for a specific application, manufacturers should take into account factors such as operating environment, load requirements, and aesthetic considerations. It is essential to work closely with experienced design engineers and material specialists to ensure that the chosen zinc die-cast knobs meet the desired performance criteria and quality standards.
“The Parts We Make Today, We Ship Today”
Kinetic Die Casting Company. Inc.
6918 Beck Avenue, North Hollywood,
California 91605, United States of America
E-mail sales@kineticdc.com
USA Toll Free: (800) 524-8083 Local: (818) 982-9200
To get prices for Die Casting Tooling Molds or Parts:
RFQ Die Casting Tooling Part Prices
Kinetic Die Casting Company makes:
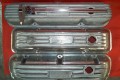
Die Casting Bracket Hardware
Airplane Die Casting Parts
Permalink: https://www.kineticdiecasting.com/kdc/zinc-die-cast-knobs/
Revolutionizing Automotive Engineering
Aluminum Car Part Die Castings are used where efficiency, performance, and safety are important, the choice of materials and manufacturing processes plays a critical role in shaping the future of vehicle design. Among the myriad manufacturing techniques available, aluminum die casting stands out as a game-changer, offering unparalleled versatility, strength, and efficiency in producing car parts. From engine components to structural elements, aluminum die castings have revolutionized automotive engineering, driving innovation and excellence in vehicle manufacturing. Let’s delve into the significance of aluminum car part die castings and explore their transformative impact on the automotive industry.
Aluminum die casting enables the production of automotive parts with intricate geometries, tight tolerances, and complex features that would be challenging or cost-prohibitive to achieve using traditional manufacturing methods. Through advanced die casting techniques such as high-pressure die casting (HPDC) and vacuum die casting, automotive engineers can create components with superior dimensional accuracy, surface finish, and mechanical properties. This precision engineering translates into enhanced performance, reliability, and durability of vehicle systems, contributing to a smoother, more responsive driving experience for consumers.
As the automotive industry continues to prioritize sustainability and environmental responsibility, aluminum die casting emerges as a preferred manufacturing solution due to its eco-friendly properties. Aluminum is highly recyclable, with the ability to be melted down and reused indefinitely without compromising its mechanical properties. By incorporating recycled aluminum into die casting processes, automakers can reduce energy consumption, greenhouse gas emissions, and raw material extraction, contributing to a more sustainable and circular economy.
Aluminum car part die castings have revolutionized automotive engineering, offering a winning combination of lightweight design, precision engineering, durability, and sustainability. As automakers continue to innovate and push the boundaries of vehicle design and performance, aluminum die casting will remain a cornerstone technology, driving progress and excellence in the automotive industry. From fuel-efficient engines to sleek body designs, aluminum die castings are shaping the future of mobility, delivering vehicles that are safer, more efficient, and more environmentally friendly.
“The Parts We Make Today, We Ship Today”
Kinetic Die Casting Company. Inc.
6918 Beck Avenue, North Hollywood,
California 91605, United States of America
E-mail sales@kineticdc.com
USA Toll Free: (800) 524-8083 Local: (818) 982-9200
To get prices for Die Casting Car Parts:
Quote Prices for Die Casting Car Parts/font>
Kinetic Die Casting Company makes:
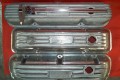
Die Casting Bracket Hardware
Airplane Die Casting Parts
Manufacturing Excellence in California
The State of California USA, renowned for its innovation, diversity, and entrepreneurial spirit, stands as a beacon of manufacturing excellence within the United States. From cutting-edge technology and aerospace advancements to sustainable practices and artisanal craftsmanship, the state’s manufacturing sector encompasses a broad spectrum of industries, each contributing to its vibrant and dynamic economy. Let’s explore the multifaceted landscape of manufacturing in California and the factors that have propelled its growth and success. Manufacturing Excellence: The Dynamic Landscape of Manufacturing in California
California’s manufacturing sector spans a diverse array of industries, reflecting the state’s rich tapestry of innovation and creativity. From Silicon Valley’s high-tech giants and biotech innovators to Southern California’s aerospace pioneers and Central Valley’s agricultural powerhouses, California is home to a multitude of manufacturing hubs driving progress and prosperity across the state and beyond. Whether it’s advanced electronics, sustainable energy solutions, precision machinery, or artisanal goods, California’s manufacturing prowess knows no bounds.
Innovation and Technology Leadership, at the forefront of innovation and technology, California’s manufacturing sector continually pushes the boundaries of what’s possible. Silicon Valley, situated in the San Francisco Bay Area, serves as the epicenter of technological innovation, driving advancements in semiconductors, software development, and digital manufacturing. With a concentration of world-class research institutions, venture capital firms, and entrepreneurial talent, California remains a global leader in fostering innovation and nurturing startups that are revolutionizing the manufacturing landscape.
Aerospace and Defense Manufacturing Excellence, Southern California boasts a rich heritage in aerospace and defense manufacturing, with iconic companies such as Boeing, Lockheed Martin, and Northrop Grumman calling the region home. From designing and manufacturing cutting-edge aircraft and spacecraft to developing advanced defense systems and components, California’s aerospace industry continues to push the boundaries of aerospace engineering and innovation. With a skilled workforce, robust supply chain, and close collaboration with government agencies and research institutions, California remains a vital hub for aerospace manufacturing excellence.
Sustainability and Green Manufacturing, California leads the nation in embracing sustainable manufacturing practices and green technologies aimed at reducing environmental impact and promoting sustainability. From renewable energy solutions and zero-emission vehicles to eco-friendly packaging and waste reduction initiatives, manufacturers across the state are pioneering innovative approaches to mitigate climate change and create a more sustainable future. With stringent environmental regulations and a commitment to corporate social responsibility, California’s manufacturing sector serves as a global model for sustainable and responsible production practices.
Skilled Workforce and Education Initiatives, California’s manufacturing success is underpinned by its highly skilled and diverse workforce, supported by a robust network of educational institutions, vocational training programs, and workforce development initiatives. From community colleges and technical schools to apprenticeship programs and industry partnerships, California invests in preparing the next generation of manufacturing talent, ensuring a steady pipeline of skilled workers equipped to meet the evolving needs of the industry. Additionally, initiatives promoting diversity, equity, and inclusion are fostering a more inclusive and equitable manufacturing workforce reflective of California’s diverse population.
Global Connectivity and Trade, As a global economic powerhouse, California benefits from its strategic location and robust trade connections, serving as a gateway to international markets. With world-class ports, airports, and logistics infrastructure, California facilitates the movement of goods and services to and from key markets around the world. International trade agreements and partnerships further enhance California’s position as a global manufacturing hub, facilitating the exchange of ideas, technologies, and resources that drive innovation and economic growth. Manufacturing in California is characterized by innovation, diversity, and a relentless pursuit of excellence. From technological breakthroughs and aerospace advancements to sustainability initiatives and workforce development, California’s manufacturing sector continues to shape the future of industry and drive economic prosperity both within the state and beyond. As innovation and collaboration thrive, California remains at the forefront of manufacturing innovation, paving the way for a brighter, more sustainable future.
“The Parts We Make Today, We Ship Today”
Kinetic Die Casting Company. Inc.
6918 Beck Avenue, North Hollywood,
California 91605, United States of America
E-mail sales@kineticdc.com
USA Toll Free: (800) 524-8083 Local: (818) 982-9200
To get prices for Die Casting Tooling Molds or Parts:
RFQ Die Casting Tooling Part Prices
Kinetic Die Casting Company makes:
Die Casting Business
Die Casting Manufacturing