How Are Diecast Heating Plates Used? Diecast heating plates are used to increase the temperature of certain objects, which are done for testing and other experimental purposes. Depending on the design and purpose of the heating plate, it can also …
Continue reading
Tag Archives: Heat Sinks
Compare Extruded Aluminum Heatsinks to Die Casting in 2023
Aluminum is the preferred material used to produce heat sinks because of aluminum’s thermal conductive properties, the weight of the many aluminum alloys and, the natural electrical conductivity of aluminum.
EXTRUSIONS AS HEAT SINKS:
Initially, heat sinks were produced as extrusions. The extrusion process is to heat aluminum to a point just before melting temperature and then “squeeze” or extrude the aluminum through a form creating long aluminum sections that will need to be cut into the proper part lengths. Then the part is machined for mounting holes and other features. There is wasted aluminum because the material cut away cannot be used in the extrusion process again. Also, many times the lengths have left over amounts that are too short to be used to make parts.
DIE CASTINGS AS HEAT SINKS:
In the die casting process, we inject aluminum into a die forming the heat sink. As a die casting part, the mounting holes and special features can be die cast into a “net shape” part. There is not wasted aluminum in the die casting process because the excess aluminum is remelted and used to form additional parts. Also in the die casting process, there are no “left over” sections.
ADVANTAGES OF DIE CASTING HEAT SINKS:
1. Machining holes and features is not necessary saving money in the production process.
2. Time is saved in manufacturing because machining is not necessary.
3. No wasted aluminum.
Kinetic Die Casting Company produces many types of aluminum heat sink parts. Contact Kinetic Die Casting Company to purchase your die casting parts or die casting tooling.
Kinetic Die Casting Company
6918 Beck Avenue North Hollywood, California, 91605, USA
800-524-8083 or 818-982-9200 or fax 818-982-0877
Kinetic Die Casting manufactures aluminum and zinc die casting parts. Samples of KDC’s work include die cast speaker parts, aluminum tile plates, and other die cast metal parts. If you would like to have a quote please visit our website: Kinetic Die Casting Company
p>Kinetic Die Casting Company. Inc.
6918 Beck Avenue, North Hollywood,
California 91605, United States of America
E-mail sales@kineticdc.com
USA Toll Free: (800) 524-8083 Local: (818) 982-9200
To get prices for Die Casting Tooling Molds or Parts:
RFQ Die Casting Tooling Part Prices
Kinetic Die Casting Company makes:
Sponsored Listings:
Aluminum Heatsinks for Your Convenience in 2023
Aluminum Heatsink
Aluminum Heat Sinks for Your Convenience. Aluminum heat sinks have the ability to absorb and disperse heat from another object through thermal contact since aluminum has good electrical and thermal properties. This amazing characteristic makes aluminum heat sinks ideal for cooling purposes. An aluminum heat sink is a piece of molded aluminum usually placed on top of a processor. In most cases, you would first have to remove the heat sink before you would be able to see the processor.
Wherever a need for effective heat dispersal exists, there will undoubtedly be aluminum heat sinks installed. Refrigeration is the foremost industry that employs the use of heat sinks. The aluminum heat sinks produced these days come in various shapes, forms and sizes. The standard heat sink though, contains long fins and thin protruding extensions for directing the heat coming from the processor to the cooler setting inside the heat sink. Majority of today’s heat sinks available in the market are furnished with fans that blow cool air towards the fins to disperse the heat more efficiently. These fans are usually situated on top or in the middle of the fins.
Die Cast Aluminum Heat Sinks are designed in such a way that less machining is necessary. The production rate averages from 250 to 2,500 heat sink parts a day. Another great think with aluminum heat sinks is that they are completely lighter than their stainless steel equivalents, having a specific gravity of 0.10 pounds per cubic inch. They are also easily grounded since aluminum is electrically conductive.
Aluminum heat sinks are used in cell phones, motor housings, circuit boards, refrigerators, airplane parts, satellite components, automotive, lighting parts, microwaves, etc.
Kinetic Die Casting manufactures products like heatsink die casting, aluminum housings, and lighting fixtures. If you would like more information, please visit our website:Kinetic Die Casting Company
Kinetic Die Casting Company 6918 Beck Avenue, North Hollywood, California 91605, United States of America
E-mail sales@kineticdc.com USA Toll Free: (800) 524-8083 Local: (818) 982-9200
To get prices for Die Casting Tooling Molds or Parts: RFQ Die Casting Part Prices
Kinetic Die Casting Company makes:
Aluminum Parts or Plastic Parts
Military Die Casting Parts
Die Casting Tooling
Blogspot Kineticdiecasting
Extruded Aluminum Heatsinks in 2023
Extruded aluminum heatsinks are made by heating aluminum to the point of a semi-solid state. Then this aluminum is pushed (extruded) through an extrusion die. These aluminum forms have the profile of the die it was pushed through, much like the play dough toy extruder. The simple shapes are stars or circles. These forms are cut to the length needed.
Aluminum Heatsinks that are extruded typically have a flat bottom and ribs on the top. They can be extruded in lengths of several feet an cut to shorter lengths. Because these extruded aluminum heatsinks were formed by pushing through a die, there is a limitation on details that can be formed on the top and bottom surfaces. If a depression is needed to mount components then it will need to be machined into the part as a pocket as an after operation, dramatically increasing the part cost. More typically, if holes are needed for mounting, they too will need to be machined into the parts as a secondary operation. Any other holes needed so wires or components can pass through have the same limitation.
The Aluminum Die Casting Process injects metal into a mold or die that forms the top, bottom and sides. Mounting holes, through holes and cavity indentations formed into the part are in the die halfs on the top and bottom. Aluminum Die Casting Heatsinks will have all the features necessary for installing the components and the holes for mounting during the original manufacturing operation. Die casting heatsinks will not require secondary operations for holes and features.
Kinetic Die Casting manufactures aluminum and zinc die casting parts. Samples of KDC’s work include die cast speaker parts, aluminum tile plates, and other die cast metal parts. If you would like to have a quote please visit our website: Kinetic Die Casting Company
Kinetic Die Casting Company 6918 Beck Avenue, North Hollywood, California 91605, United States of America
E-mail sales@kineticdc.com USA Toll Free: (800) 524-8083 Local: (818) 982-9200
To get prices for Die Casting Tooling Molds or Parts: RFQ Die Casting Part Prices
Kinetic Die Casting Company makes:
Automotive Die Casting Parts
Die Casting Bracket Hardware
Airplane Die Casting Parts
Zinc Die Casting Company California
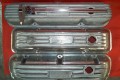
Extruded Aluminum Heatsinks in 2022
Extruded aluminum heatsinks are made by heating aluminum to the point of a semi-solid state. Then this aluminum is pushed (extruded) through an extrusion die. These aluminum forms have the profile of the die it was pushed through, much like the play dough toy extruder. The simple shapes are stars or circles. These forms are cut to the length needed.
Aluminum Heatsinks that are extruded typically have a flat bottom and ribs on the top. They can be extruded in lengths of several feet an cut to shorter lengths. Because these extruded aluminum heatsinks were formed by pushing through a die, there is a limitation on details that can be formed on the top and bottom surfaces. If a depression is needed to mount components then it will need to be machined into the part as a pocket as an after operation, dramatically increasing the part cost. More typically, if holes are needed for mounting, they too will need to be machined into the parts as a secondary operation. Any other holes needed so wires or components can pass through have the same limitation.
The Aluminum Die Casting Process injects metal into a mold or die that forms the top, bottom and sides. Mounting holes, through holes and cavity indentations formed into the part are in the die halfs on the top and bottom. Aluminum Die Casting Heatsinks will have all the features necessary for installing the components and the holes for mounting during the original manufacturing operation. Die casting heatsinks will not require secondary operations for holes and features.
Kinetic Die Casting manufactures aluminum and zinc die casting parts. Samples of KDC’s work include die cast speaker parts, aluminum tile plates, and other die cast metal parts. If you would like to have a quote please visit our website: Kinetic Die Casting Company
Heat Sink Die Castings
Chocolate Fountain Die Castings
Die Casting Heat Sinks
Die Casting Heat Sink Pictures
Golf Products Die Castings
Kinetic Die Casting Company 6918 Beck Avenue, North Hollywood, California 91605 USA
E-mail sales@kineticdc.com Toll Free: (800) 524-8083 Local: (818) 982-9200 Fax: (818) 982-0877
Die Casting Heat Sink Prices
What is Aluminum Heatsink in 2022
What is an Aluminum Heatsink? A Heat sink is an object that ingests and disperses heat which comes from another object by direct or radiant thermal contact. Heat sinks are often used in various functions wherein effective heat dispersion is needed. Few examples are lasers, cooling electronic apparatus, heat engines and refrigeration. You can often see an Aluminum Heat sink attached to a computer’s circuit board.
A common Heat Sink have a collection of fin-like or comb projections and a single or more than two surfaces. These properties of a heat sink increases its outer face area which touches the air, and as a result, the heat dispersion percentage increases. Since aluminum heat sinks are known to be static objects, a fan is used to help heat sinks by giving better airflow.
Aluminum is usually used in making heat sinks because this is the perfect material that conducts heat, and it is also lighter and cheaper than other materials. The main advantage of Aluminum Heatsinks is that they may be shaped through the process of extrusion effortlessly, which is why they make the difficult cross sections achievable. The base area of the Aluminum Heatsinks should be smooth and even to guarantee the most advantageous thermal connection together with the other object which needs cooling.
If you match up the process used to make the Aluminum Heatsinks to other Die Casting Heat sink processes, you’ll notice that it only involves less machining, and cooling fins may actually be done while setting up the holes. Additionally, the Aluminum Heatsinks possess a great dimensional constancy.
Kinetic Die Casting manufactures aluminum and zinc die casting parts. Samples of KDC’s work include die cast speaker parts, aluminum tile plates, and other die cast metal parts. If you would like to have a quote please visit our website: Kinetic Die Casting Company
Kinetic Die Casting Company 6918 Beck Avenue, North Hollywood, California 91605, United States of America
E-mail sales@kineticdc.com USA Toll Free: (800) 524-8083 Local: (818) 982-9200
To get prices for Die Casting Tooling Molds or Parts: RFQ Die Casting Part Prices
Kinetic Die Casting Company makes:
Automotive Die Casting Parts
Die Casting Bracket Hardware
Airplane Die Casting Parts
Zinc Die Casting Company California
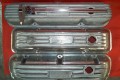