1. Why Should you Use Aluminum Hardware Brackets? The use of aluminum hardware brackets is becoming more and more popular than that of their steel counterparts. Why is that so? Well, basically, the reasons can be unending. From its flexibility …
Continue reading
NADCA – North American Die Casting Association
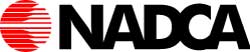
Kinetic Die Casting Company is a corporate member of the North American Die Casting Association NADCA. We have been corporate members for a very long time. The North American Die Casting Association (NADCA) is the sole trade and technical association of the die casting industry. NADCA membership consists of both corporate and individual members from over 950 companies located in every geographic region of the U.S.
These companies include custom die casters (who produce die castings for sale to others), captive die casters (who produce castings for their own use in manufacturing a product), and suppliers to the die casting industry. NADCA members can be found in every type of community across the nation, representing both rural and urban interests.
The North American Die Casting Association (NADCA) represents the voice of the die casting industry. NADCA is committed to promoting industry awareness, domestic growth in the global marketplace and member exposure. Headquartered in Wheeling, IL, the association is comprised of both individual members and corporate members located throughout United States, Canada and Mexico.
The North American Die Casting Association (NADCA) also has an extensive government relations program based in Washington D.C. The program provides government affairs services to NADCA members. NADCA relies on the services of Waterman & Associates to act as the ears, eyes and voice of the die casting industry at the federal level.

The Basics of Die Casting Alloys
The Basics of Die Casting Alloys. Die-casting is very comparable to permanent mold casting, only that the metal which is pushed into the mold experiences higher pressures which total to 10-210Mpa (1,450-30,500) psi. Because of this, the exterior of the die-cast is very fine; the dimensions are also much more precise at 0.2% of casting dimension.
Die-casting may be done in two different ways, either utilizing a cold chamber method or by employing a hot chamber procedure. Both vary in the time exposure of the melt which certain metals need either more or less. Cold chamber procedures are typically utilized for aluminum and copper, also counting its fellow die casting alloys. The metal is located in the cold chamber for each shot and requires less time exposure of the melt. Hot chamber methods normally are utilized for metals that have low melting points and high fluidity. This includes zinc, tin and lead. The die cavity is located permanently in the melted metal. The inlet port of the pressurizing cylinder is exposed as the plunger moves to its opening position. This permits a different charge of melted metal to fill the cavity.
Aluminum, Zinc and Copper are the die casting alloys that are chiefly utilized in die-casting for a variety of reasons. Die-castings are restricted from 20kg to a maximum that is reliant on the metal. Large castings typically have superior porosity problems because of the trapped air and the premature hardening of the die-cast cavity. In essence, many things must considered when performing die-casts in order to make certain the excellence of the metals. Die casting alloys guarantee excellent quality and a great finish.
Kinetic Die Casting is located in North Hollywood,California. KDC specializes in manufacturing zinc and aluminum alloy casting parts. If you would like a quote, please visit our website:Kinetic Die Casting Company
Die Casting Aerospace Parts
Kinetic Die Casting Company makes several types of Die Casting Aerospace Parts. These aerospace die casting parts are used for many types of purposes. Some of these parts are used on many types of aircraft, such as: airplanes, jet planes or helicopters.
Aircraft manufacturers typically specify aluminum die casting to make the aerospace parts because aluminum is lightweight and inexpensive as well as very strong.
- Lightweight – Aluminum weighs only .098 pounds each cubic inch of material as compared to zinc which weighs about 2.44 pounds each cubic Inch.
- Inexpensive – Aluminum is the third most common element on earth, so it is more available than other materials. Aluminum is used in over 80% of all die castings produced in the world.
- Strong – Aluminum parts can be geometrically designed to be stronger than steel. Look up “aluminum is stronger than steel” on Google to see the results.
These aerospace parts range from: airplane engine piston heads, airplane distributor cap housings, fuel system parts, detention ring parts, cargo loading housings, lighting fixture parts, electronic enclosures, electronic housings, motor housings and various other aluminum die casting parts.
The companies that trust us to purchase their die casting parts from Kinetic Die Casting Company are many.
- Here are a few of the aircraft and aerospace companies that we can name:
- Robinson Helicopter
- Ancra International
- Whittaker Controls
- AAR Cargo Systems
- Boeing Aerospace
- Barry Controls
- Meggitt Aerospace
- Parker Hannifin Aerospace Corporation (Parker FSD)
- Circle Seal Aerospace
- Kelly Aerospace
- Curtiss Wright
- Honeywell
- United Technologies Aerospace
Low Quantities.
Many of these companies order lower quantities. One of the companies listed here will order less than 50 parts at a time. Many of these companies order 250 parts or less. Kinetic Die casting will accept any purchase order quantity.
Contact Kinetic Die Casting Company when you need any of the following: Low Quantities, Great Quality, Fast Delivery.
Kinetic Die Casting Company
6918 Beck Avenue
North Hollywood, CA 91605
Drumheller Industries is Closed (Die Casting Company)
Drumheller Industries is Closed (Zinc Die Casting Company) – Today I drove past the building of Drumheller Industries on 10967 Tuxford Street in Sun Valley, California. I was saddened that the building is for sale. Drumheller Die Casting Company was a zinc die casting company that was in business over 40 years. Scott Drumheller, the last owner of the company, told me his grandfather started the company by building special hot chamber zinc die casting machines. These machines will cast and trim the zinc die casting parts automatically so that the parts drop into buckets.
For over two years, I talked to Scott about the possibility of purchasing his company. He has had declining sales and fewer customers every year. The value of his company was dropping. Unfortunately, Scott felt he needed a job but did not want to work for another die casting company. He wanted to continue Drumheller operations until he had to stop.
In July 2012, Scott Drumheller told me he needed to pay either a penalty or a fine to the state of California to stay in business. This fee was vary large, and amounted to more than 10% of his annual sales. He decided to close Drumheller Industries unless someone would purchase his corporation from him and his liability to the state of California.
I offered to pay him a sales commission and two or three times the value of his equipment for his equipment and his customers. He insisted that the corporation ownership needed to be part of the package. I do not understand how it could benefit him to scrap his equipment for one third of the amount of money that I offered to pay him and why he believed I would take his corporate liabilities or even why he thought it was fair to insist the corporate transfer as part of the package. We could not come to an agreement and he chose to scrap his equipment instead of selling the die casting machines to Kinetic Die Casting Company.
Another California Die Casting Company has closed. This is very sad to me. There are less than one third of the die casting companies in California as there were 20 years ago.
The good news to me is that my company, Kinetic Die Casting Company, is thriving and growing while other companies are declining and closing. Our customers feel safe buying their parts from us. We purchased the mold bases and die casting tooling from the Drumheller die casting auction to service their customers.

Optimal Die Casting Production Part Quantity
Optimal Die Casting Production Part Quantity? “I need to buy several thousands of parts to buy die castings”. That is the most common myth or false belief people have regarding the optimal die casting part production quantity. We believe, the optimum production quantity of die casting parts is, the quantity of parts you need to buy.
Unfortunately, many die casting companies also believe the “high quantity only” myth. Some die casting companies perpetuate that myth to force their customers into buying more parts than they need. They refuse smaller quantity purchase orders unless their customers pay a very high “set-up charge”. Sometimes, they will push out delivery of lower part quantities to over 12 weeks, in an effort to dissuade the lower quantity part purchase orders. Then sometimes the part quality is “lacking” but the parts are needed so badly, the sub-quality parts are accepted because we do not have 12 more weeks to wait for replacement parts.
Kinetic Die Casting is thrilled to accept die casting part purchase orders of any quantity. We will accept part purchase orders with deliveries of 10,000 parts or less. Many of our part purchase orders have part deliveries of less than 1,000 parts. In fact, many of our aerospace part purchase orders have deliveries of less than 100 parts and sometimes less than 10 parts.
Our part deliveries range from four to six (4-6) weeks for raw castings. No matter what quantity you want, as long as it is less than 10,000 parts. In most cases we will ship your parts in less than six weeks, if we do not need to wait for outside processes to hold up our part delivery.
In most production part purchase orders, we ship your parts the day we make your parts. We do not have departmental delays that can take several days or weeks to process the parts after the parts are produced.
Our optimal die casting part production quantity, is the quantity you want to buy. Contact us today for a competitive price. Your delivery will be less than six weeks.
Kinetic Die Casting Company
818-982-9200
sales@kineticdc.com